AIOU Course Code 9544 Question Paper Spring 2025
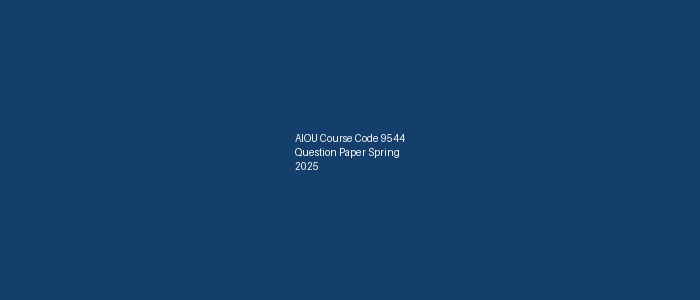
ALLAMA IQBALOPEN UNIVERSITYISLAMABAD
(Department of Business Administration)
WARNING
- PLAGIARISM OR HIRING OF GHOST WRITER(S) FOR SOLVING THE ASSIGNMENT(S) WILL DEBAR THE STUDENT FROM THE AWARD OF DEGREE/CERTIFICATE IF FOUND AT ANY STAGE.
- SUBMITTING ASSIGNMENT(S) BORROWED OR STOLEN FROM OTHER(S) AS ONE’S OWN WILL BE PENALIZED AS DEFINED IN THE “AIOU PLAGIARISM POLICY”.
Course: Inventory and Material Management (9544) Semester: Spring, 2025
Level: PGD
Total Marks: 100 Pass Marks: 50
ASSIGNMENT No. 1
Note: All questions carry equal marks.
Q. 1 What are the essentials of sales and operating systems? Discuss with examples. (20)
Q. 2 What is the relationship between material management and supply chain? Discuss with examples. (20)
Q.3 What are the various steps of material requirements planning? Discuss with examples. (20)
Q. 4 What is the sequence of operation in material management? Discuss with examples. (20)
Q. 5 Explain break-even analysis. How does break-even analysis help the manager in decision-making? Discuss with examples. (20)
Total Marks: 100 Pass Marks: 50
ASSIGNMENT No. 2
This assignment is a research-oriented activity. You are required to select one of the following topics according to the last digit of your roll number. For example, if your roll number is D-3427185 then you will select topic number 5 (the last digit). Visit any business/commercial organization and write a paper of about 1000 words on the topic allotted to you.
The report should follow the following format:
- Title page
- Acknowledgments
- An abstract (one-page summary of the paper)
- Table of contents
- Introduction to the issue (brief history & significance of issue assigned)
- Practical study of the organization (with respect to the issue)
- Data collection methods
- SWOT analysis (strengths, weaknesses, opportunities & threats)relevant to the issue assigned
- Conclusion (one-page brief covering important aspects of your report)
- Recommendations (specific recommendations relevant to the issue assigned)
- References (as per APA format)
- Annexes (if any)
GUIDELINES FOR ASSIGNMENT # 2:
- 1.5 line spacing
- Use headers and subheads throughout all sections
- Organization of ideas
- Writing skills (spelling, grammar, punctuation)
- Professionalism (readability and general appearance)
- Do more than repeat the text
- Express a point of view and defend it.
Course: Inventory and Material Management Course Code: 9544
Level: PGD Credit Hours: 03
Unit No. 1 Overview of Material Management and Production Plan
1.1 The Concept of Material Management
1.2 The Nature of Operating Environment
1 .3 Materials Management and Supply Chain relationship
1 .4 Understanding Supply Chain Metrics
1.5 Establishing Production Planning System
1.6 Manufacturing Planning and Control System
1 .7 Essentials of Sales and Operation Planning
1 .8 Manufacturing Resource Planning vs. Enterprise Resource Planning
1.9 Production Plan Formulation and Implementation
Unit No. 2 Master Scheduling and Material Requirements Planning
2.1 Introduction to Scheduling
2.2 Master Scheduling and Production Plan
2.3 Master Production Schedule Formulation
2.4 Linkage of Production Planning, Master Scheduling, and Sales
2.5 Significance of Material Requirements Planning
2.6 Structure of Material Bills
2.7 Material Requirements Planning Process
2.8 Examining Material Requirements Plan
Unit No. 3 Capacity Management and Production Activity Control
3.1 Capacity Planning and Management
3.2 Essentials of Capacity Requirements Planning
3.3 Capacity Available vs Capacity Required
3.4 Scheduling Orders Scheduling
3.5 Balancing capacity available and load
3.6 The concept of Production Activity Control
3.7 Data Requirements and Order Preparation
3.8 Scheduling, Load Leveling and Bottlenecks
3.9 Theory of Constraints and Drum-Buffer-Rope
3.10 Order Release Process
3.11 Input/Output Control
3.12 Operation Sequencing
3.13 Preparing Production Reporting
Unit No. 4 Purchasing
4.1 Importance of Purchasing for Supply Chain Management
4.2 Purchasing Objectives and Purchasing Cycle
4.3 Essential Requirements for Purchasing
4.4 Functional Specification Description
4.5 The Process of Supplier Selection
4.6 Price Determination and Break-Even Analysis
4.7 Material Requirements Planning and Purchasing Relationship
4.8 Purchasing as a Component of Supply Chain Management
4.9 Customer Relationship Management
4.10 Supplier Relationship Management
Unit 5: Forecasting
5.1 Introduction to Forecasting and Demand Management
5.2 Key Characteristics of Demand
5.3 Principles of Forecasting
5.4 Collection and Analyzing Data
5.5 Forecasting Methods
5.6 Seasonalvs Deseasonal Demands
5.7 Tracking the Forecast
Unit No. 6 Inventory Management and Order Quantities
6.1 Introduction to Inventory Management
6.2 Objectives of Inventory Management
6.3 Aggregate Inventory Management
6.4 Differentiating Inventory Management from Aggregate Inventory Management
6.5 Inventory and Material Flow
6.6 Supply and Demand Patterns
6.7 Buffering Effects of Inventories
6.8 Calculating Inventory Costs
6.9 Preparing Financial Statements
6.10 Financial Statements and Inventory
6.11 ABC Inventory Classification System
6.12 Introduction to Order Quantities
6.13 The Concept of Economic Order Quantity (EQQ)
6.14 Economic Order Quantity (EQQ) in Practice and Variations
6.15 Quantity Discounts and Period Order Quantity (PQQ)
6.16 Order Quantities for Product Lines
Unit No.7 Independent Demand Ordering Systems and Physical Control
7.1 Introduction to Independent Demand Ordering Systems
7.2 The Concept of Order Point System
7.3 Safety Stock Estimation
7.4 Service Level Decisions
7.5 Forecasting and lead-Time Intervals
7.6 Role of Two-Bin System and Kanbans for Order Point
7.7 Periodic Review System
7.8 Structure of Distribution Inventory
7.9 Physical Inventory and Warehouse Management
7.10 Overview of Warehouse Management
7.11 Elements of Physical Control and Security
7.12 Usefulness of Inventory Record Accuracy
7.13 Technology Applications for Inventory Control and Storing
Unit No. 8 Physical Distribution and Process Design
8.1 Introduction Physical Distribution System
8.2 Important Interfaces adding Value
8.3 Transportation and its different Types
8.4 For-Hire vs Not-for-Hire Carriers
8.5 Elements of Transportation Costs
8.6 Warehousing, Packaging and Materials Handling
8.7 Usefulness of Multi-Warehouse Systems
8.8 Product Life Cycle
8.9 Principles of Product Development
8.10 Product Specification and Design
8.11 Process Design and Nesting Concept
8.12 Factors Influencing Process Design
8.13 Classification of Processing Equipment
8.14 Organizing Process Systems
8.15 Costing in Processing Systems
8.16 Continuous Process Improvement
Unit No. 9 Quality Principles and Practices
9.1 Just-in-Time (JIT) Philosophy
9.2 Causes of Waste and Solutions
9.3 Key Elements of Just-in-Time Environment
9.4 Manufacturing Planning and Control in a JIT Environment
9.5 The Concept, Tools and Techniques of Lean Production
9.6 Kanban, Drum-Buffer-Rope and Hybrid Systems
9.7 The Concept of Quality
9.8 Key Elements of Total Quality Management (TQM)
9.9 Cost of Failure and Controlling Quality
9.10 Output Variability
9.11 Process Capability and Process Control
9.12 Sample Inspection and Sampling Plan
9.13 The International Organization for Standardization (ISO) 9000:2000
9.14 Significance of Concept of Benchmarking and Six Sigma
9.15 Executing Quality Function Deployment
9.16 Integrating JIT, TQM, and MRP-II
Recommended Books: